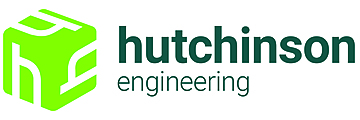
-
Contact: Susan Wiseman
-
susan@hutchinsonengineering.co.uk
-
+44(0)7745 115883
-
www.hutchinsonengineering.co.uk
-
Everite Road
Widnes
WA8 8PT
Cheshire
- Size
- SME
- Direct employees
- 150
- Turnover (reported)
- £27,666,912
- Regional Markets
- Europe
- Nuclear Contracting Tiers
- Tier 5: Processors & Fabricators
Tier 4: Sub-component Suppliers/Distributors
Accreditations
F4N Case Studies
Hutchinson Engineering Ltd
Steel Fabrications
Design, manufacture, coating, secondary fit-out and installation of complex steel structures to ISO1090-2 EXC4.
Overview
Established in 1979, Hutchinson are an SME based in North-West England, offering the design, manufacture, coating, secondary fit-out and installation of complex steel structures. Our strength is in the ability to provide a diverse scope, utilising in-house resources and experience in a production-flow workshop environment, enabling efficient and cost effective supply to a high quality-assured standard. .
To support our activities, we hold accreditation to UKCA BS EN ISO1090-2 EXC4, ISO14001, ISO45001 & ISO3834-2
Our business ethos is to maintain a range or capabilities across the steel fabrication scope, developing in-house resource, expertise and facilities allowing us to meet our clients timescale, quality and project demands every time.
Products and Services
Product | Sector |
---|---|
Fabrication Hi-integrity & Complex Structures including Heavy | Nuclear Civil |
Structural Fabrications | Nuclear Civil |
Containment Structure | Nuclear Civil |
Access Ladders Stairs & Platforms | Nuclear Civil |
Coatings Paints Protection Processes & Systems | Nuclear Civil |
Apparatus | Nuclear Civil |
Blast and Security Doors and Materials | Nuclear Civil |
Crane, heavy lifting, and rigging | Nuclear Civil |
Civil Works & Civil Engineering | Nuclear Civil |
Containment Structure | Nuclear Civil |
Containment System Fabrications | Nuclear Civil |
Custom equipment for heavy load handling | Nuclear Civil |
Fabrication Cutting Forming Pressing & Bending - Equipment | Nuclear Civil |
Fabrication Cutting Forming Pressing & Bending - General Civil Works | Nuclear Civil |
Fabrication Cutting Forming Pressing & Bending - Modules & Skid Mounted Systems | Nuclear Civil |
Fabrication Cutting Forming Pressing & Bending - Support & Critical Structural Items | Nuclear Civil |
Fabrication Med-integrity Structures | Nuclear Civil |
Ferrous and Non ferrous Materials - General Engineering | Nuclear Civil |
Flasks Casks & Containers including Transport | Nuclear Civil |
Fuel Transfer Equipments | Nuclear Civil |
Machining - General Engineering | Nuclear Civil |
Pond Furniture, Racks & Storage Fabrications | Nuclear Civil |
Pond & Pool Liner Fabrications | Nuclear Civil |
Sheet metal fabrication | Nuclear Civil |
Shield Doors and Radiation Protection Fabrications | Nuclear Civil |
Structures | Nuclear Civil |
Steelwork including Mezzanine & Gantry Systems | Nuclear Civil |
Transfer Devices | Nuclear Civil |
Transportation Casks, Flasks & Systems | Nuclear Civil |
Waste Storage Containers Casks Flasks & Systems - High Level Waste | Nuclear Civil |
Waste Storage Containers & Systems - Low & Intermediate Level Waste | Nuclear Civil |
Workshop Equipment | Nuclear Civil |
Our maximum overhead-crane lifting capacity is 50t, located at our quay-side workshop in Liverpool, supported by our secondary coating facilities at the quayside, enabling us to load-out larger items directly onto the Mersey.
We maintain plate rolling facilities (cans 4.2m diameter, 3m long and upto 40mm thick), together with SAW Growing-lines capable to producing tubular sections upto 60t . Our Coating facility supports this production area enabling coating of items upto 30m in length.
We are able to offer Structural and Detailed design works, including 3D modelling.
We are able to carry out secondary-process activities associated with steel structures, such as cabling, RF equipment and testing, minor electrical works, fall-arrest systems, etc . . . This activity is prevalent in our structure supply for the mobile telecoms industry.
We maintain Site-Based installation and erection teams to support our activities.
Site Facilities
Shop Floor
10000m2 10,000m2 across four locations including quayside loadout facility. Additional 6 acres of storage yards. Our Coating Facilities include Shot-Blasting & Climate-controlled Paint Booth (max size 30m x 5.5m x 5.5m), metalization and sweep-blast facilities.
Specialist Machinery
Capability | Swing | Length | Width | Weight | |
---|---|---|---|---|---|
Horizontal Mill / TurnCNC Lathe with Y Axis; 18″ x 23″ (457 x 584 mm) max capacity, 4.0″ (102 mm) bar, 31.75″ (806 mm) swing, ±2.00″ (±50.8 mm) Y-axis travel, 40 hp (29.8 kW) vector drive, 3200 rpm, A2-8 spindle, 12″ (305 mm) chuck, 12-station BMT-65 turret. | Min: | - | - | - | N/A |
Max: | 806mm | 584mm | 457mm | 1500kg | |
Vertical Turning (Conventional)Webster & Bennett 36” E-R series Vertical Turning and Boring Machine | Min: | - | - | - | N/A |
Max: | 1219mm | 1016mm | - | 1500kg |
Welding & Cladding
Capability | Swing | Length | Width | |
---|---|---|---|---|
Gas Tungsten Arc Welding (GTAW)manual | Min: | - | - | - |
Max: | - | - | - | |
Manual Metal Arc Welding (MMA) | Min: | - | - | - |
Max: | - | - | - | |
Metal Active Gas Welding (MAG)manual, solid wire and cored wire | Min: | - | - | - |
Max: | - | - | - | |
Metal Inert Gas Welding (MIG)manual | Min: | - | - | - |
Max: | - | - | - | |
Submerged Arc Welding (SAW)mechanised, Column and boom with max reach 5m, tractors | Min: | - | - | - |
Max: | 5000mm | - | - |
Inspection / Testing
- CMM machines
- Non destructive testing - Magnetic Partical
- Non destructive testing - Radiography
- Non destructive testing - Ultrasonic
- Proof Load Testing
Design
- CAD Design - 2D
- CAD Design - 3D
- CAM Design - 2D
- CAM Design - 3D
Recent Work
UKAEA, European Spallation Source Active Cells Transport and Assembly Frame
Hutchinson was commissioned by the UKAEA to design and deliver a high-integrity transport lifting frame for the European Spallation Source, a major science project in Sweden. Meeting stringent specifications and tight deadlines, we utilised advanced manufacturing techniques to ensure timely delivery of this critical component
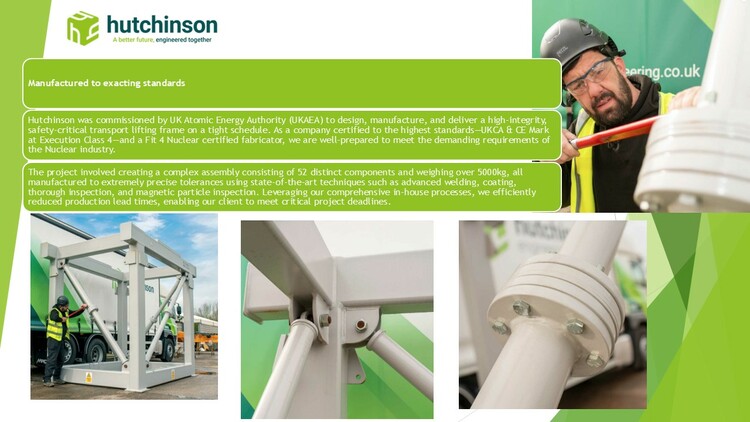
Cranes manufactured specifically to Konecranes unique operational requirements.
Hutchinson began manufacturing overhead cranes in September 2022 and since then we have supplied over 100 cranes, spanning up to 28.5m wide. These cranes feature complex steelwork, high-spec coating requirements and varied levels of electrical work, all of which we are able to provide in-house. Hutchinson’s comprehensive in-house capabilities in electrical engineering, steelwork fabrication, and specialised coating processes have been crucial in meeting the demanding requirements of this project. The collaboration has not only reinforced Hutchinson’s manufacturing expertise but has also strengthened our ability to handle large-scale, technologically advanced projects.
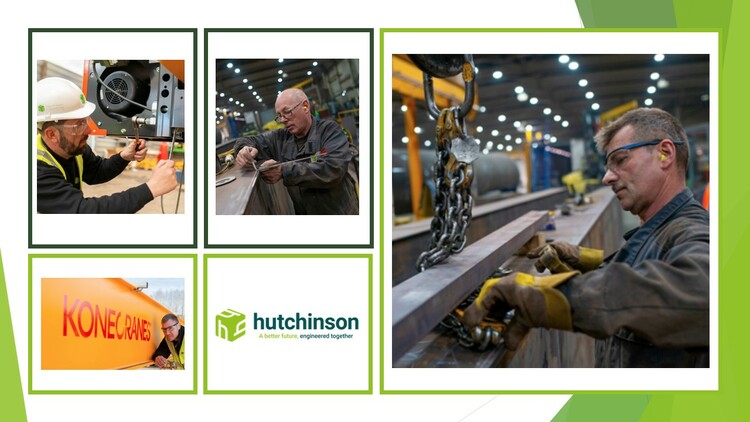