-
Contact: Gareth Monkhouse
-
gareth.monkhouse@tsp-engineering.co.uk
-
01900 842778
-
www.tsp-engineering.co.uk
-
Curwen Road
Derwent Howe
Workington
CA14 3YX
Cumbria
- Size
- SME
- Direct employees
- 200
- Turnover (reported)
- £20,000,000
- Regional Markets
- Asia, Europe
- Nuclear Contracting Tiers
- Tier 3: Original Equipment Manufacturing Organisations
Tier 2: Systems Integration Organisations
Accreditations
TSP Engineering Ltd.
Heavy Fabrications
Design, Fabrication, Machining, Assembly and Testing
Overview
Since its inception in 1945, TSP Engineering's Workington Facility has built up extensive knowledge and experience in delivering demanding projects within the Nuclear, Defence, Steel, Industrial and Oil / Gas Industries. These projects have typically involved design, manufacture, testing and commissioning of large scale plant and machinery to an exacting quality standard.
TSP has specialist resources dedicated towards the cost-effective manufacture and maintenance of heavy industrial plant and equipment. The workshop currently operates 16 hours a day, 5 days a week and is available all year round with the flexibility to switch to 24 hour, 7 day working when demands require it. This provides a unique capability to carry out modifications or adjustments to plant and equipment should problems be encountered during testing and customer witnessing of equipment on our site. Thereby allowing manufacturing specific programmes and delivery schedules to suit customer requirements.
The main TSP facility comprises of 19,200 square metres of shop floor capacity, 2 x 5 metre deep manufacturing pits and a maximum lifting capability of 130 tonnes, utilised by a team of highly skilled personnel within the areas of machining, fabrication, shot blasting and painting, heat treatment, assembly and testing.
Products and Services
Product | Sector |
---|---|
Fire Alarms Detection Enclosures & Panels | Nuclear Civil |
Fabrication Med-integrity Structures | Nuclear Civil |
Structural Fabrications | Nuclear Civil |
Fabrication Med-integrity Structures | Nuclear Defence - Naval Marine |
Structural Fabrications | Nuclear Defence - Naval Marine |
Fuel Transfer Equipment | Nuclear Civil |
Fuel Transfer Equipment | Nuclear Defence - Naval Marine |
Precision & General Machining | Nuclear Civil |
Precision & General Machining | Nuclear Defence - Naval Marine |
Mechanical & Electrical Engineering (M&E) | Nuclear Civil |
Storage Racks & Furniture including Pond | Nuclear Civil |
Shielding | Nuclear Civil |
Shielding | Nuclear Defence - Naval Marine |
Flasks Casks & Containers including Transport | Nuclear Civil |
Flasks Casks & Containers including Transport | Nuclear Defence - Naval Marine |
Containers Transportation & Storage | Nuclear Civil |
Precision & General Machining | Nuclear Civil |
Precision & General Machining | Nuclear Defence - Naval Marine |
Pressure Vessels Heat Exchangers & Tanks including Internals | Nuclear Civil |
Containers Transportation & Storage | Nuclear Civil |
Containers Transportation & Storage | Nuclear Defence - Naval Marine |
Welding & Welding Systems | Nuclear Civil |
Welding & Welding Systems | Nuclear Defence - Naval Marine |
Please visit our website for further information on our products and capabilities - www.tsp-engineering.co.uk
Site Facilities
Shop Floor
19200m2
Specialist Machinery
Capability | Swing | Length | Width | Weight | |
---|---|---|---|---|---|
Horizontal Milling (CNC)Giddings and Lewis Horizontal Borer | Min: | - | - | - | N/A |
Max: | 1500mm | 1500mm | 1500mm | - | |
Horizontal Milling (CNC)Giddings and Lewis MC60 CNC Twin Pallet Horizontal Machining Centre | Min: | - | - | - | N/A |
Max: | 1500mm | 2000mm | 2000mm | - | |
Horizontal Milling (CNC)Giddings and Lewis G60F CNC Horizontal Floor Borer | Min: | - | - | - | N/A |
Max: | 2500mm | 6000mm | 3000mm | - | |
Horizontal Milling (CNC)Giddings and Lewis G60 CNC Horizontal Machining Centre | Min: | - | - | - | N/A |
Max: | 2500mm | 4250mm | 3050mm | - | |
Horizontal Milling (CNC)Giddings and Lewis G50 CNC Horizontal Machining Centre | Min: | - | - | - | N/A |
Max: | 2000mm | 2500mm | 2500mm | - | |
Horizontal Milling (CNC)Giddings and Lewis G40 CNC Horizontal Machining Centre | Min: | - | - | - | N/A |
Max: | 2000mm | 2500mm | 2000mm | - | |
Horizontal Milling (CNC)Asquith Horizontal Floor Borer | Min: | - | - | - | N/A |
Max: | 2000mm | 6000mm | 3000mm | - | |
Horizontal Milling (CNC)Giddings and Lewis A130 CNC Horizontal Machining Centre | Min: | - | - | - | N/A |
Max: | 1500mm | 1500mm | 1500mm | - | |
Horizontal Milling (Conventional)Scharmann Horizontal Floor Borer | Min: | - | - | - | N/A |
Max: | 3000mm | 7800mm | 5000mm | - | |
Horizontal Turning (CNC)Small Heyligenstaedt CNC Turning Centre | Min: | - | - | - | N/A |
Max: | 480mm | 2000mm | 250mm | - | |
Horizontal Turning (CNC)Large Heyligenstaedt CNC Turning Centre | Min: | - | - | - | N/A |
Max: | 720mm | 3000mm | 475mm | - | |
Horizontal Turning (Conventional)Dean Smith and Grace Lathe | Min: | - | - | - | N/A |
Max: | 500mm | 3100mm | 330mm | - | |
Horizontal Turning (Conventional)VDF Lathe | Min: | - | - | - | N/A |
Max: | 2000mm | 10500mm | 1750mm | - | |
Vertical Milling (CNC )Wadkin III CNC Vertical Machining Centre | Min: | - | - | - | N/A |
Max: | 1000mm | 3500mm | 2300mm | - | |
Vertical Milling (CNC )Stirk Vertical CNC Machining Centre | Min: | - | - | - | N/A |
Max: | 2750mm | 6100mm | 3400mm | - | |
Vertical Milling (Conventional)Butler Elga Mill | Min: | - | - | - | N/A |
Max: | 1200mm | 2000mm | 970mm | - | |
Vertical Milling (Conventional)Kendall and Gent Plano Mill | Min: | - | - | - | N/A |
Max: | 1800mm | 6000mm | 1800mm | - | |
Vertical Milling (Conventional)Webster and Bennett Vertical Borer | Min: | - | - | - | N/A |
Max: | 1500mm | 1350mm | 800mm | - | |
Vertical Mill / TurnGray 300 Series Double Column Twin RAM Vertical CNC Boring Machine | Min: | - | - | - | N/A |
Max: | 5200mm | 3050mm | - | - |
Welding & Cladding
Capability | Swing | Length | Width | |
---|---|---|---|---|
Gas Tungsten Arc Welding (GTAW) | Min: | - | - | - |
Max: | - | - | - | |
Manual Metal Arc Welding (MMA) | Min: | - | - | - |
Max: | - | - | - | |
Metal Active Gas Welding (MAG) | Min: | - | - | - |
Max: | - | - | - | |
Metal Inert Gas Welding (MIG) | Min: | - | - | - |
Max: | - | - | - | |
Narrow Gap Welding (GTAW or SAW) | Min: | - | - | - |
Max: | - | - | - | |
Orbital & Planetary (GTAW & SAW)We have no orbital processes but we do have the ability to rotate/manipulate and fixed head TIG, Flux Core and SAW weld. | Min: | - | - | - |
Max: | - | - | - | |
Submerged Arc Welding (SAW) | Min: | - | - | - |
Max: | - | - | - |
Inspection / Testing
- Electrical
- Equipment Qualification
- Non destructive testing - Magnetic Partical
- Non destructive testing - Radiography
- Non destructive testing - Ultrasonic
- Pressure / Hydro Testing
- Proof Load Testing
Design
- CAD Design - 2D
- CAD Design - 3D
- CAM Design - 2D
- CAM Design - 3D
Recent Work
MSSS Refurbishment of Packages and Gamma Gates
The MSSS Package is used for the transfer of waste materials. TSP Engineering in Workington was awarded a contract to carry out the modification, rebuild, testing and commissioning of 8 off Packages and 5 off Gamma Gates.
The package receipt area on the Gamma Gate was clad with stainless steel and re-machined. New locking mechanisms were incorporated into the side plates and the electrical trunking was modified to bring it in line with the latest specifications.
The Gamma Gates underwent cladding, machining, shot blast and painting. Following which they were then assembled and transferred to the Test Rig to undergo a rigorous test schedule and Works Acceptance Testing.
A purpose built test rig was erected, including an in-house designed and manufactured test panel, to functionally test the Packages and Gamma Gates prior to delivery.
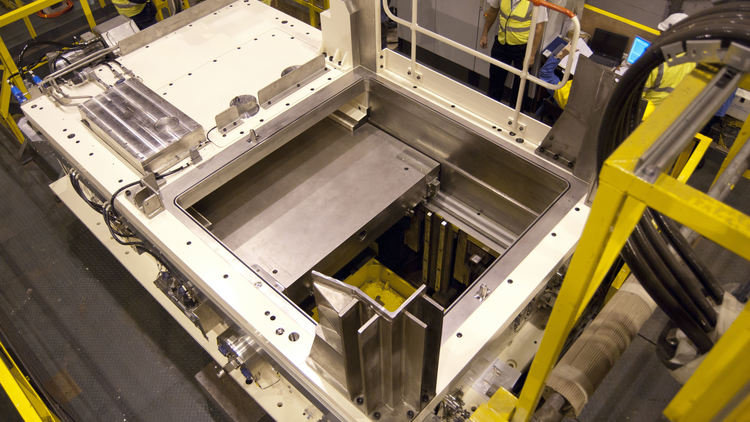