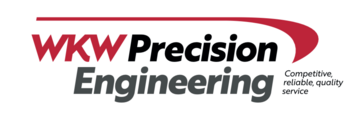
-
Contact: Adrian Wyatt
-
adrain@wkw-eng.co.uk
-
01422 351720
-
www.wkw-eng.co.uk
-
Shaw Royd Works
Shaw Lane
Halifax
HX3 9HD
West Yorkshire
- Size
- SME
- Direct employees
- 32
- Turnover (reported)
- £3,500,000
- Regional Markets
- Asia, Africa, Australia, Europe, North America, South America
- Nuclear Contracting Tiers
- Tier 3: Original Equipment Manufacturing Organisations
Tier 4: Sub-component Suppliers/Distributors
Accreditations
WKW Precision Engineering Co Ltd
Precision Machining
C.N.C. Milling-C.N.C. Turning-E.D.M. Wire & Spark Erosion- Gear Cutting- Hardness & NDE. Inspections- Co-Ordinate Measuring Inspections-Horizontal Machining, Grinding-Internal & External Grinding-Surface Grinding-Splines-Straight & Helical Gears-Serrations-Keyways-Broaching.
Overview
WKW Precision Engineering is Yorkshire’s trusted partner in high-tolerance precision manufacturing. With over 40 years of industry expertise, we specialise in tailored solutions for sectors including nuclear, oil and gas, medical, and subsea exploration.
Our commitment to quality, sustainability, and safety is reinforced through certifications such as ISO 9001, ISO 14001, ISO 45001 and Fit 4 Nuclear (F4N) accreditation. We are proud members of Made in Yorkshire, The Supply Chain Charter for Nuclear Decommissioning Sites, and the Calderdale and Kirklees Manufacturing Alliance (CKMA), as well as sponsors of the West Yorkshire Manufacturing Service.
We provide bespoke services, including CNC milling, turning, gear cutting, and advanced inspection, ensuring every component is manufactured to the highest standards. From concept to completion, we deliver precise, reliable, and cost-effective solutions, helping our clients succeed globally.
Why are we Unique:
Comprehensive Capabilities: Offering a full suite of machining services including CNC milling, turning, gear cutting, grinding, EDM, and advanced inspection, ensuring complete solutions for complex projects.
Industry Accreditations and Expertise: With ISO 9001, ISO 14001, ISO 45001 and Fit 4 Nuclear (F4N) accreditation, WKW stands out as a leader in quality, environmental sustainability, and safety in the engineering sector.
Collaborative Industry Engagement: As members of Made in Yorkshire, The Supply Chain Charter for Nuclear Decommissioning Sites, and the Calderdale and Kirklees Manufacturing Alliance (CKMA), plus sponsors of the West Yorkshire Manufacturing Service, WKW is deeply embedded in regional manufacturing development and nuclear sector innovation.
Products and Services
Product | Sector |
---|---|
Precision & General Machining | Nuclear Civil |
Precision & General Machining | Oil & Gas including LNG |
Precision & General Machining | Aerospace - Civil and Defence |
Precision & General Machining | Petrochemical & Refining |
Precision & General Machining | Subseas and Offshore |
We also manufacture from damaged components and without the need for initial drawings. Through reverse engineering and utilising 3D modelling software we undertake projects giving you accurate technical drawings and high-quality renovated parts that match your original requirements
We also have the capability to carry out Surface Finish, Hardness Testing using Rockwell & Brinell Methods and NDE Surface and Volumetric Testing. All covered under our Accreditation ISO9001:2015.
Site Facilities
Shop Floor
10000m2
Specialist Machinery
Capability | Swing | Length | Width | Weight | |
---|---|---|---|---|---|
3 Axis Milling | Min: | - | - | - | N/A |
Max: | - | 1020mm | 610mm | - | |
4 Axis Milling | Min: | - | - | - | N/A |
Max: | - | 1020mm | 610mm | - | |
Horizontal Mill / Turn | Min: | - | - | - | N/A |
Max: | - | 4000mm | 615mm | - | |
Vertical Milling (CNC ) | Min: | - | - | - | N/A |
Max: | - | 610mm | 610mm | - |
Inspection / Testing
- Clean room facilities
- CMM machines
- Equipment Qualification
- Non destructive testing - Magnetic Partical
- Non destructive testing - Ultrasonic
- Temperature controlled facility for inspection
Design
- CAD Design - 3D
- CAM Design - 3D